Step inside the workshop
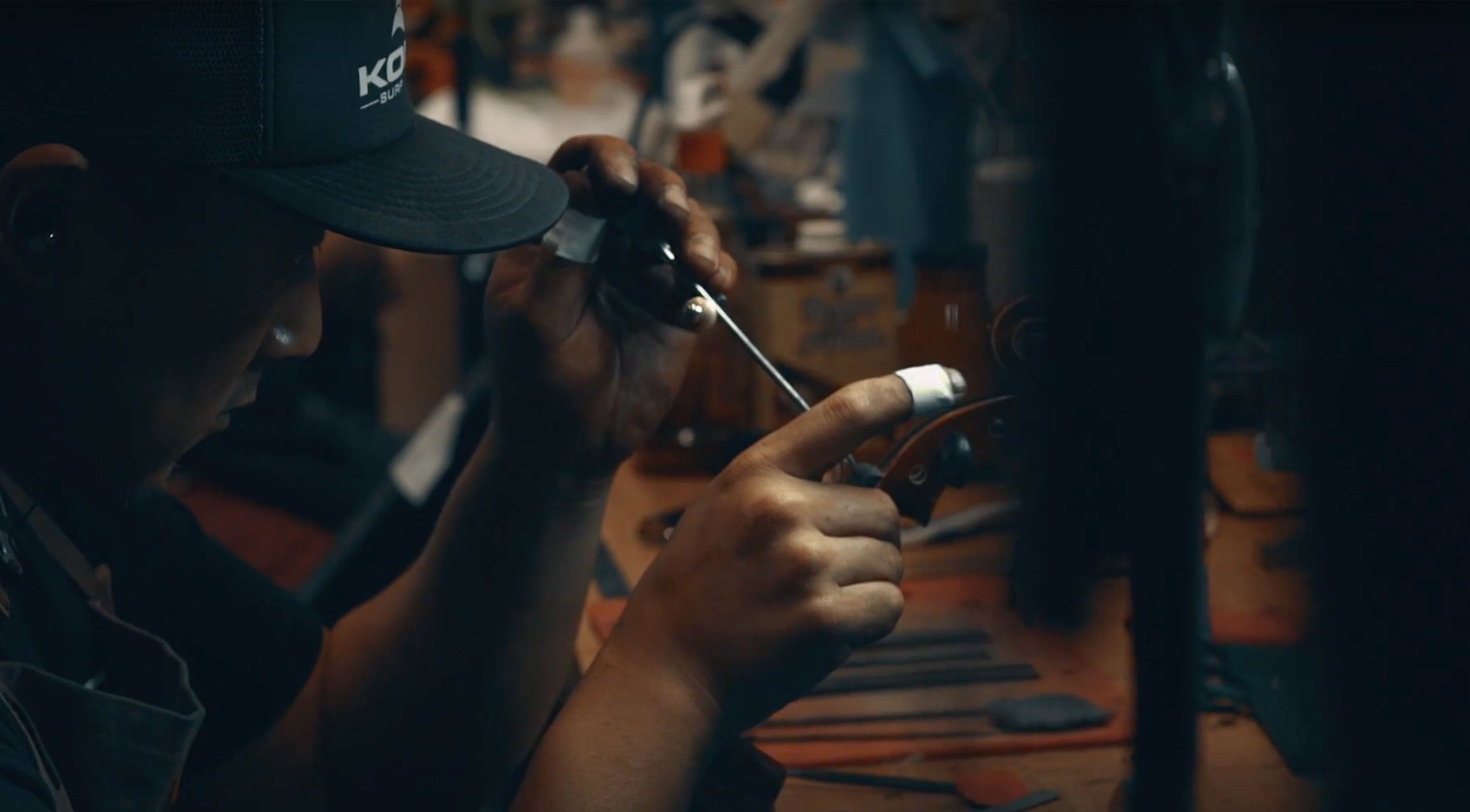
From day one, we have devoted ourselves to more than setting up instruments, but also setting up every customer for success.
That’s why Fiddlershop’s talented team of luthiers inspect, adjust, and test every instrument to ensure that it reaches its fullest potential before being delivered to you.
10-Point Setup Process
1. Structural Inspection
As the first step in our 10-point setup process, we inspect the construction of the interior blocks, linings, bass bar, and meticulously look for any cracks or open seams. This ensures that the instrument is built to last and can sound its best.
2. Pegs
The tuning pegs are shaped and fitted to the pegbox. We apply a peg compound to ensure that they turn easily, quietly, and hold firmly.
3. Nut
The nut is shaped to the correct height and the string grooves are spaced and carved evenly to ensure finger placement feels natural. We apply graphite to lubricate the string grooves, which allows the string to gently pass through the groove without causing damage to the string.
4. Fingerboard
The fingerboard is planed and shaped to the ideal curvature and thickness. Any indentations or depressions are removed to facilitate a smooth and accurate playing experience. Our fingerboards are only made from a fine selection of ebony wood.
5. Bridge
The bridge is responsible for transferring the vibrations of the strings to the body of the instrument. Each bridge is carved by hand and fitted individually to each instrument. A properly fitted bridge allows the strings to vibrate freely without touching the fingerboard while maintaining a comfortable height for ease of playing. If necessary we install string parchment under the thinnest string, to prevent the string from digging into the bridge over time.
6. Soundpost
Luthiers call the soundpost the soul of the instrument. The placement and the fit of the soundpost can dramatically change an instrument’s personality. We cut and place each soundpost to reach our expectations of the instrument’s potential, and also make adjustments to accommodate any customer requests.
7. Tailpiece
The tailpiece is connected to the end button with a high quality tail gut. The tailgut length is adjusted to bring the vibrating string length and afterlength to the optimal specification.
Most instruments are set up with a single fine tuner on the tailpiece that matches the pegs, endbutton and chinrest. On many student instruments though, a composite tailpiece with fine tuners on all strings may be used to simplify tuning, and to reduce weight.
8. Strings
We choose a set of strings that will complement the instrument as well as the player's individual needs. We only use high quality strings from well-known string makers.
9. Testing & Final Inspection
We test every instrument for playability and sound quality to make sure it meets or exceeds all specification expectations. At this step, one of our highly qualified players works closely with the luthiers to make very fine adjustments and re-test. If an instrument doesn't pass testing, it is brought back to the bench for further adjustments.
10. Final Cleaning
We want every instrument to look its best when it arrives at your door. We wipe off any smudges or rosin dust from testing, and use a gentle polish if necessary so that the instrument sparkles when you open the case.